Online Application | Application Status | Oxygen Concentrator Supply Scheme 2021
The life-sustaining gas is oxygen, and the need for oxygen has increased dramatically during the covid-19 pandemic.
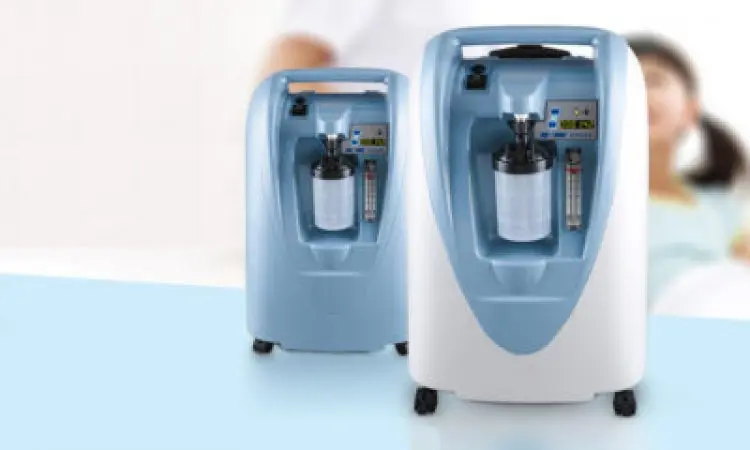
Online Application | Application Status | Oxygen Concentrator Supply Scheme 2021
The life-sustaining gas is oxygen, and the need for oxygen has increased dramatically during the covid-19 pandemic.
Oxygen is the life-supporting gas and in the time of the covid-19 pandemic, the need for oxygen has increased considerably. In the past month during the second wave of covid-19, the Government of Odisha has taken various steps to control the spread of the virus. There are many people across the state that require oxygen. So, in order to meet the demand for oxygen and make it available to all the needy citizens, the Government of Odisha has launched an Oxygen Concentrator Supply Scheme. Through this scheme, the government is going to deliver oxygen concentrators to the doorstep of patients. In this article, we have covered all the important details regarding this scheme like what is the oxygen concentrator supply scheme? its objective, benefits, features, eligibility criteria, required documents, application procedure, etc. By reading this article you will know how you can avail the benefit of this scheme.
The chief minister of Odisha Mr. Naveen Patnaik launched the oxygen concentrator supply scheme on 7th June 2021. This scheme has been launched due to the covid-19 pandemic as oxygen is believed to be the force that prevents the life of those patients who are severely infected by the covid-19 virus. Through Oxygen Concentrator Supply Scheme the government is going to provide oxygen concentrators at the doorsteps of the patients. In order to get the benefit of this scheme, the applicant has to book concentrators on the state government dashboard or on the state covid portal. The Government of Odisha started this scheme for 5 metros of the state that including Bhubaneswar, Cuttack, Brahmapur, Rourkela, and Sambalpur.
The main objective of oxygen concentrator supplies is to provide oxygen concentrators at the doorstep of the patients who are seriously infected by the covid- 19 virus and have breathing issues. Through the implementation of this scheme, the precious lives of people will be saved. As of now the relatives of patients are not required to visit hospitals in order to get oxygen concentrators. They are just required to apply online and the concentrator will be delivered to their doorstep. This will save a lot of time and timely treatment of the patient will be ensured.
Portable medical oxygen concentrators (MOCs) have found wide use in facilitating home-based oxygen therapy for patients suffering from lung conditions including COVID-19, chronic obstructive pulmonary disease (COPD), chronic bronchitis, and pneumonia, among others. To produce pure oxygen from ambient air at small scales, several adsorbent technologies based on pressure swing adsorption (PSA) have been commercialized Therefore, a majority of MOCs rely on a PSA process with a nitrogen-selective adsorbent. According to the World Health Organization (WHO), medical-grade oxygen has oxygen concentrations between 90 and 96% V/V with remaining nitrogen and argon. In alignment with these specifications, the typical oxygen product obtained from adsorption-based MOC devices consists of 90–93% oxygen at a production rate of less than 10 L/min.
In adsorption-based MOCs, due to limited adsorption capacity, the adsorbent is periodically regenerated for efficient utilization. To facilitate continuous oxygen supply, either the product oxygen can be collected in a surging column and supplied at a constant time-averaged rate, or a multi-bed operation can be utilized. Skarstrom-type PSA cycle configuration is typically utilized in MOCs, which consists of production, depressurization, purge, and pressurization steps. Based on the pressure levels of production and purge steps, three different subclasses of PSA exist that is pressure swing adsorption, vacuum swing adsorption (VSA), and pressure vacuum swing adsorption (PVSA) MOCs leverage rapid cycling of the adsorption column to maximize adsorbent utilization and miniaturize the size of the operation. In addition, small adsorbent particle sizes are used to reduce the mass transfer resistance and enhance the adsorption kinetics.
For medical use, depending on the condition of end-use patients and whether the patient is at rest or active, the required specifications of oxygen products could vary both in terms of flow rate and purity. In addition, the same oxygen concentrator unit can be used for several different patients in a hospital setting. Therefore, it is desirable to design a flexible and modular PSA process that can rapidly switch between different operating regimes for on-demand oxygen production while fulfilling different product specifications. To meet the time-varying oxygen demand, we envision a cyber-physical system (CPS) within which the blood oxygen concentration of a patient suffering from a lung condition is constantly monitored, and necessary actions to modify the operation of MOC are taken in real-time (Fig).
Benefits And Features Of Oxygen Concentrator Supply Scheme
- The chief minister of Odisha Mr. Naveen Patnaik has launched an oxygen concentrator supply scheme due to the covid-19 pandemic
- This scheme has launched on 7th June 2021
- Through this scheme, the government is going to provide oxygen concentrators at the doorsteps of the patients
- In order to get the benefit of this scheme applicant has to book the concentrator on the state government dashboard or the state covid portal
- As of now, the Government of Odisha has started this scheme in 5 metros which include Bhubaneswar, Cuttack, Brahmapur, Rourkela, and Sambalpur
- Now Citizens of Odisha require to visit hospitals in order to get the oxygen concentrators
- They can get the concentrators sitting at their home by just applying at the official website
- This will save a lot of time and timely treatment of the patients will ensure.
- Only the citizens of Odisha can take the benefit from the oxygen concentrator supply scheme
- Through the implementation of this scheme, the precious life of people will save.
- This scheme will prove to be a boon in controlling the spread of the covid-19 virus
Eligibility Criteria and Required Documents
- The patient must be currently residing in Odisha
- Adhaar card
- Ration card
- RTPCR Report
- Prescription of the Doctor in which should be clearly mentioned that the patient requires oxygen support
- Passport size photograph
- Mobile number
- Address proof
Procedure To Login On The Portal
- Visit the official website of the state dashboard, Odisha
- The home page will open in front of you
- On the homepage, you are required to click on the O2 concentrator booking tab
- Now you are required to click on apply now
- After that under the already registered section, you have to enter your registered mobile number
- Now you have to click on the login
- After that, a dialogue box will appear on your screen
- On this dialogue box, you have to click on send OTP
- Now you will receive an OTP on your registered mobile number
- You have to enter the OTP into the OTP box
- After that, you have to click on the login
- By following this procedure you can log in to the portal
Do Administrator Login
- First of all, go to the official website
- of the state dashboard, Odisha
- The home page will open in front of you
- Now you have to click on the O2 concentrator booking tab
- After that, you are required to click on apply now
- Now you have to click on the Admin option
- After that, a new page will appear before you
- On this new page, you have to enter your username and password
- After that, you have to click on the login
- By following this procedure you can do an administrator login
To meet the aforementioned processing objectives, several literature studies focus on using different adsorption cycles and materials for performing air separation. The table summarizes the process characteristics and performance metrics for different literature studies. Farooq et al. performed simulation and experimental studies to investigate a 2-bed 4-step PSA process for air separation using 5A zeolite. The theoretical results showed that oxygen products with 93.4% purity can be obtained, albeit at a low oxygen recovery of 20.1% and a low production rate of 0.07 L/min. To increase the air separation efficiency, Kopaygorodsky et al. evaluated the viability of ultra-rapid PSA cycles using 5A zeolite. It was observed that 85% oxygen product with a product recovery of 60% could be obtained with a total cycle time of fewer than 3 seconds and for a small BSF of 0.0073, thereby leading to more compact and efficient PSA units. Santos et al. performed simulation and optimization studies for studying 4-step PSA and PVSA cycles for oxygen production with three different candidate adsorbents, i.e., Oxysiv 5, Oxysiv 7, and SYLOBEAD MS S 624. Their analysis indicated that Oxysiv 7 had the best separation performance for both PSA and PVSA cycles with 94.5% oxygen purity, 21.3% recovery, and a 3.7 L/min production rate. They further extended their analysis to investigate a 6-step PSA cycle for small-scale medical applications, and obtained a 94.5% pure oxygen product with 34.1% recovery and 4.3 L/min production rate.
In the envisioned CPS, a blood oxygen saturation sensor transmits the recorded data to a controller. The controller checks the patient’s status, and if there is a requirement of modifying oxygen specifications due to a change in the patient’s health condition or activity, optimal control actions are determined and transmitted to the MOC. The MOC is accordingly reconfigured to adjust oxygen production flow rate and purity. Within this real-time data-based flexible PSA operation, one of the most challenging tasks is to determine the optimal control action policies and predict the dependence of outlet product specifications on input control actions. Specifically, it is challenging to optimally design and operate PSA columns due to their inherent nonlinear dynamics, complex process operation, and variable operating regimes. For optimal operation, several decision variables need to be evaluated which include cycle configuration and operation, pressure levels, purging conditions, and bed regeneration efficiency. In addition, there are several objectives that need to be met which include modularity, compactness, reliability, and efficiency.
Therefore, minimizing the BSF leads to lower adsorbent inventory levels and smaller MOC units. On the other hand, oxygen recovery is computed by calculating the fraction of oxygen recovered in the product outlet relative to the amount of oxygen fed during a PSA cycle at a cyclic steady state. Consequently, for a given product specification, a higher oxygen recovery leads to lower compression costs and lower ambient air feed flow rates. As MOC is a small-scale device with a limited adsorbent amount and rapid cycling, there is a high energy consumption due to frequent pressure variation as compared to conventional PSA operation. However, for small-scale applications, the relative simplicity and reliability of MOC play a more significant role as compared to energy consumption. Overall, the key design goals while developing PSA-based MOC are (1) increasing adsorbent productivity, (2) enhancing oxygen recovery, and (3) developing compact and lightweight units.
Moreover, different zeolites can be used in conjunction with different PSA cycle configurations to develop air separation processes with varying performance and product specifications. Even though these adsorbents generally have a high working capacity and nitrogen/oxygen selectivity, there still exist significant variations in their adsorption isotherms, heats of adsorption, particle density, and mass transfer resistances.
These material-specific characteristics, when coupled with different cyclic configurations and operating conditions, can lead to significant differences in process performance. Therefore, to perform an extensive PSA flexibility analysis, we leverage the simulation-based optimization framework to evaluate the impact of varying material properties, cyclic configuration, bed design, and operating conditions on process performance. The optimization studies are performed for candidate adsorbents including LiX, LiLSX, and 5A zeolites in combination with both PSA- and PVSA-type cycles.
Moreover, different zeolites can be used in conjunction with different PSA cycle configurations to develop air separation processes with varying performance and product specifications. Even though these adsorbents generally have a high working capacity and nitrogen/oxygen selectivity, there still exist significant variations in their adsorption isotherms, heats of adsorption, particle density, and mass transfer resistances. These material-specific characteristics, when coupled with different cyclic configurations and operating conditions, can lead to significant differences in process performance. Therefore, to perform an extensive PSA flexibility analysis, we leverage the simulation-based optimization framework to evaluate the impact of varying material properties, cyclic configuration, bed design, and operating conditions on process performance. The optimization studies are performed for candidate adsorbents including LiX, LiLSX, and 5A zeolites in combination with both PSA- and PVSA-type cycles.
Here, we solve the process simulation model for the design and optimization of PSA- and PVSA-based MOCs with varying performance levels. The major focus is to evaluate different candidate adsorbents (i.e., LiX, LiLSX, 5A) and cycle operating conditions on the process performance metrics which include oxygen product purity and recovery, production rate, and BSF. For given product specifications, a higher oxygen recovery and lower BSF improve the process economics. Depending on the application at hand, a specific set of operating conditions and adsorbents can be used to meet desired objectives.
Before performing the optimization case studies, several simulations are performed to generate process simulation data, visualize the process performance metrics, and obtain a reasonably good initial guess for optimization case studies. The MATLAB function LHS design is utilized for generating a set of space-filling input simulation points using Latin hypercube sampling, which consists of varying air feed flow rate, step pressure levels and duration, purge flow rate, and adsorbent packing density.
Compared to LiX and LiLSX adsorbents, 5A zeolite has substandard process performance, especially in terms of oxygen purity obtained, due to lower nitrogen/oxygen selectivity and equilibrium adsorption capacity. Despite using 90% pure oxygen for purge and pressurization steps, the process is unable to meet the oxygen purity requirements with maximum purity observed only being 78.2% and 85.7% for PSA and PVSA, respectively. In addition, Fig. shows conservative estimates of oxygen purity obtained using 5A with 90% pure oxygen purge and pressurization, and further simulations with low-purity purge and pressurization streams indicated that the 5A-based adsorption process is unable to produce high-purity oxygen. Consequently, we do not consider 5A as a prospective candidate adsorbent in forthcoming optimization case studies.
Name Of The Scheme | Oxygen Concentrator Supply Scheme |
Launched By | Government Of Odisha |
Beneficiaries | Citizens Of Odisha |
Objective | To Provide Oxygen Concentrator At The Doorstep Of Patients |
Official Website | Click Here |
Year | 2021 |
Mode Of Application | Online |
State | Odisha |
Scheme Type | Government Scheme |